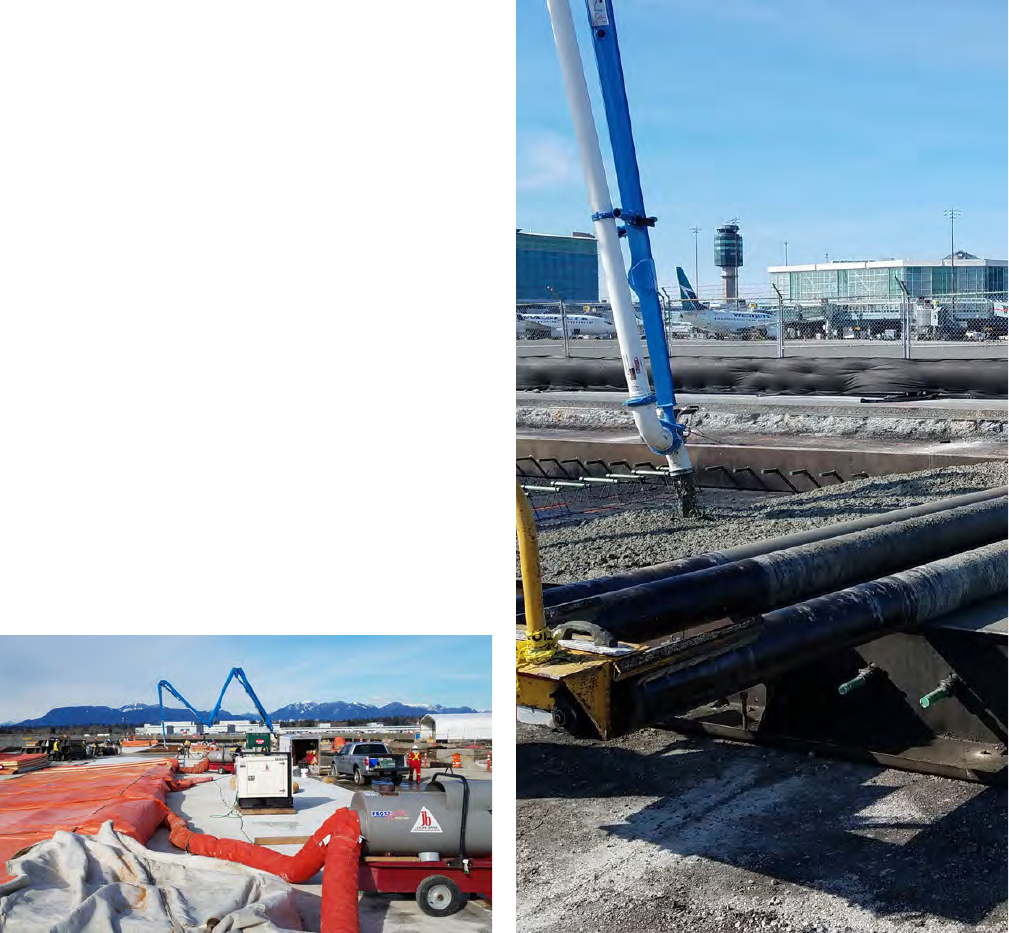
CCE Awards, YVR - East Apron VI Remote Stands | 3
Innovation
Vancouver International Airport (YVR) has experienced
significant strain on its facilities over the past several years
from unprecedented growth in passenger numbers, more
flights, and new airlines entering the market. With growth
far exceeding forecasts, a solution was urgently needed to
handle the expected traic. By working together with YVR
stakeholders, Hatch developed a fast-track solution during
the planning stage – a new remote apron, completed within
two years, providing ten AGN IIIb (i.e. Airbus A320), two AGN V
(i.e. Boeing B777), and one AGN IV (i.e. Boeing B767) aircra
stands.
Delivering a major airfield project in two years that provides
a new concept of operations for YVR was a significant
challenge with continually changing and developing
stakeholder requirements. In some cases, requirements
were either not clearly associated with or even more
stringent than published aerodrome standards, which led
to significant changes throughout design and construction.
Nevertheless, Hatch provided a safe and sustainable design
for the public while still meeting the requirements of the
Owner.
One of the most important time- and cost-saving decisions
made by Hatch was to reuse and recycle the existing
in-situ asphalt pavement structure as a subbase layer.
This significantly minimized the need for excavation and
hauling of material osite, leading to major cost, time, and
environmental benefits. Existing asphalt at the airport owned
long-term parking was milled and le in place, and the apron
was raised to ensure enough depth for a suitable pavement
structure and utility network for aircra loading and apron
operations.
The new raised apron structure was supported by a
lockblock retaining wall using mainly salvaged blocks from
existing structures. The design and construction of the
lockblock retaining wall minimized disposals and need
of new processed materials, and hence cost and time,
compared to a conventional retaining wall structure.
Another important aspect that greatly benefited the overall
project schedule was the wet- and cold-weather paving
performed during the winter construction period. Most
paving work at YVR is performed during the summer months
to ensure the best quality of work is delivered. With the
fast-track schedule of this project, a suitable winter weather
paving methodology was put in place to ensure that identical
paving work was delivered within the specifications expected
by the Airport Authority. Following the methodology
prepared by Hatch, almost four-hundred concrete slabs for
the wide-body stands were poured during the winter months
without aecting the integrity and performance of the
pavement.
Winter weather paving in sub-zero temperatures to meet the fast-
tracked project delivery schedule
Concrete paving for the new wide-body stands with minimal
disruption to active taxiways and aircra gates